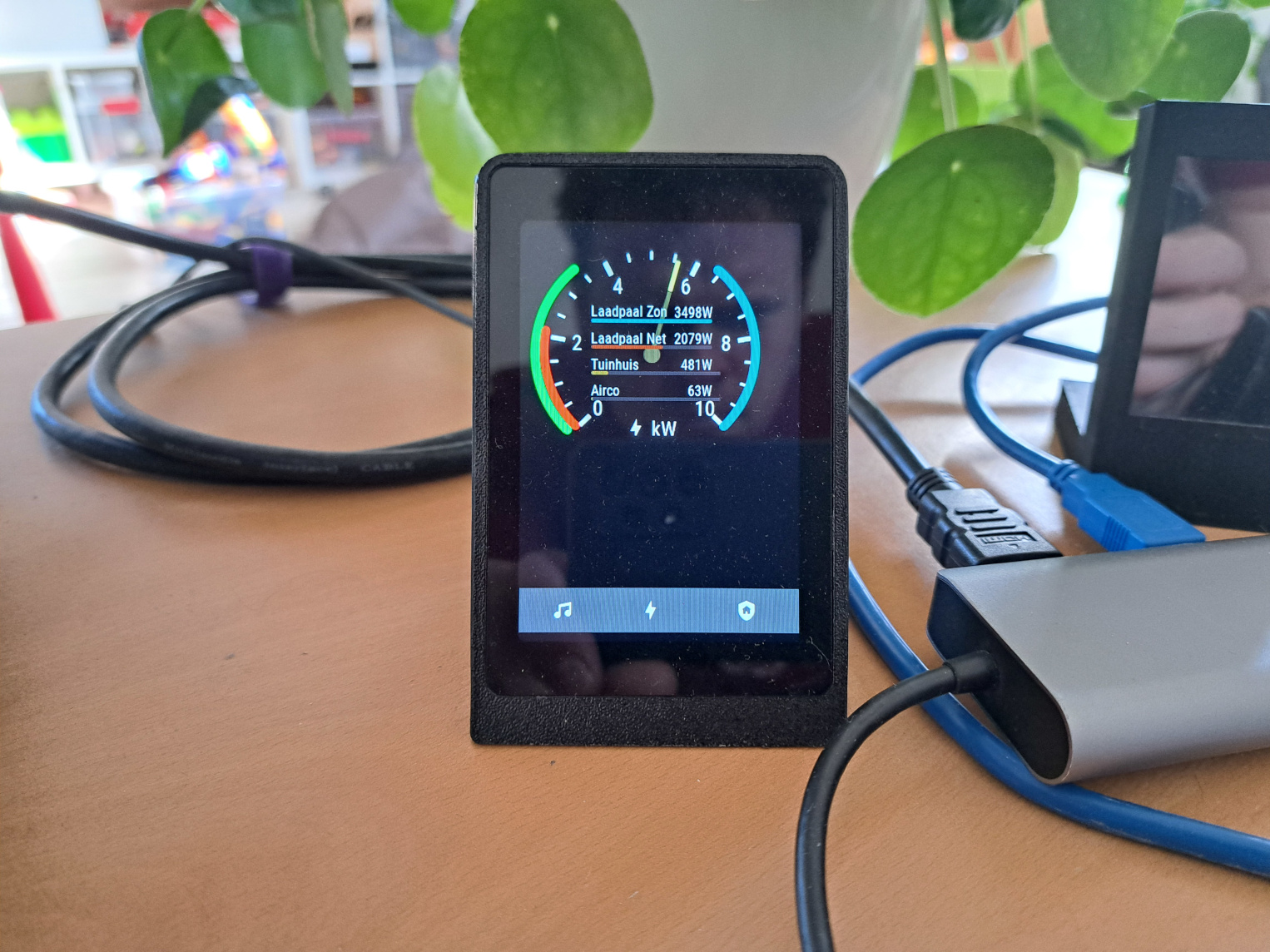
Hi, I'm Thomas, welcome to my homepage!
This is where I document some of the things I create as a hobby. Topics include electronics, hardware, software, designing, hacking, making and 3D printing. Enjoy and don't hesitate to say hi!
Hi, I'm Thomas, welcome to my homepage!
This is where I document some of the things I create as a hobby. Topics include electronics, hardware, software, designing, hacking, making and 3D printing. Enjoy and don't hesitate to say hi!